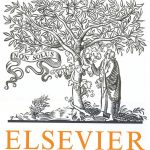
ترجمه مقاله نقش ضروری ارتباطات 6G با چشم انداز صنعت 4.0
- مبلغ: ۸۶,۰۰۰ تومان
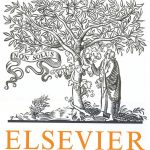
ترجمه مقاله پایداری توسعه شهری، تعدیل ساختار صنعتی و کارایی کاربری زمین
- مبلغ: ۹۱,۰۰۰ تومان
abstract
The first step in the Theory of Constraints (TOC) methodology is to identify the constraint. Several methods have been recommended in literature, such as looking for a backup of inventory (i.e., the operation that the inventory is waiting for is the constraint), or using linear programming or other analytical models. Yet, these methods may not be useful in a matured lean environment, which may have moving assembly lines where constraints are not obvious. This paper proposes three new methods for this purpose. The first method, Flow Constraint Analysis, takes a holistic view and evaluates whether the customer's demand is being satisfied. This evaluation is made by comparing the takt times and the cycle times of resources in the manufacturing system in order to identify the constraint(s). The second method, Effective Utilization Analysis, can be employed to pinpoint the location of the system constraint to a specific process or station. The actual production throughput is compared against the ideal capacity of the system to locate the bottleneck. This method is based on the relationship between WIP, bottleneck rate and lead time for a constant work in process (CONWIP) system. The third method, Quick Effective Utilization Analysis, can be used when there is little or no historical line performance data available. A case study of these methods applied to an actual production facility is presented.
5. Discussion and conclusionsIn this paper, three methods have been proposed to locate constraints in matured lean systems, especially with moving assembly lines, which usually do not have obvious bottlenecks. A case study on a real production system shows that three methods can be used for analysis at both system level and component level. The uses of the three methods are slightly different as discussed below (Table 4). The Flow Constraint Method provides the users with the ability to determine the location of the enterprise constraint. If the there are multiple system constraints they can be quickly identified.
The flow constraint method can also be used to evaluate if the design intention of the manufacturing system is being met. The Flow Constraint Method is more suitable for early planning phases, such as before the manufacturing system has been installed or when there are plans to increase the capacity of an existing facility.
The Effective Utilization Method requires more computations and data. This means the user of this method will have to spend more time and effort implementing this method. The users of this method will have the ability to narrow the focus of changes to an actual process. The users will also have deeper understandings of the manufacturing system and the effects model complexity and downtime have on the system. The Effective Utilization Method is more applicable for use as part of continuous improvement program.
The Quick Effective Utilization method requires very little computation and data. Real-time data is collected and analyzed. The analysis method can be used in situations where downtime data is not available for the production line, during verification of a simulation model or to model other resources of the manufacturing system after the primary bottleneck has been identified.
The presented case study covers only a portion of a production system. For future study, the method can be applied to the other areas of the system as well as other cases. This research can be further extended to include other aspects of the TOC methodology. After the constraint is identified, appropriate decisions can be made on exploiting the constraint to further improve the system. Insights into the system constraints can also facilitate redesigning a segment of or the whole system to be compliant with the concepts of TOC.