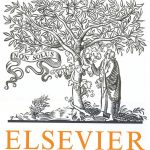
ترجمه مقاله نقش ضروری ارتباطات 6G با چشم انداز صنعت 4.0
- مبلغ: ۸۶,۰۰۰ تومان
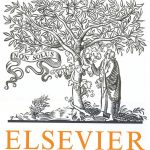
ترجمه مقاله پایداری توسعه شهری، تعدیل ساختار صنعتی و کارایی کاربری زمین
- مبلغ: ۹۱,۰۰۰ تومان
Abstract
Open holes or cutouts have been commonly used in composite structures for various engineering purposes. This paper aims to investigate the load bearing behavior and failure characteristics of the square weave carbon fiber reinforced plastic (CFRP) tubes with open holes subjected to axial compression. Effects of hole size, hole shape and hole distribution on failure modes and mechanical behaviors were evaluated experimentally and numerically. Different with the progressive crushing mode seen in the intact CFRP tubes, mid-height collapse and unstable local buckling were observed in the axial crushing tests. The peak load and specific energy absorption (SEA) of the perforated tubes decreased by around 3–22% and 26–57%, respectively, compared to those of the intact CFRP counterparts. It was found that the effect of hole size on failure strength in tubes was less sensitive than that in perforated composite laminates, but was relatively stronger than the perforation shape and distribution. The damage mechanisms were explored in-depth using strain gauge tests and finite element analysis, which showed a significant increase in shear stress around the holes prior to final failure.
4. Conclusions
This paper presented an experimental and numerical study on the failure mechanism and crushing characteristics of perforated square CFRP tubes fabricated by the bladder molding process. The representative load-displacement curves, failure modes and effect of hole size, shape and distribution on compressive behavior of perforated CFRP tubes were investigated. The differences of failure characteristics between the perforated and intact tubes were summarized. The mechanisms of crack initiation and propagation were also analyzed numerically. Within the limitation of the study, the following conclusions can be drawn: (1) Unlike the progressive crushing observed in the intact CFRP tubes, the mid-height collapse (mode I) and unstable local buckling (mode II) of perforated CFRP tubes were observed in the axial crushing tests, leading to around 3–22% reduction in the first peak force and 26–57% reduction in SEA. (2) The effect of hole size on failure strength was evaluated by the simple hole-insensitive and hole-sensitive failure criteria. The failure strength of the tube decreased by 3–22% in the presence of the hole, which represented a relatively lower reduction compared to the perforated laminates. (3) The diameter of circular hole had certain influence on the peak load by decreasing 3–22% when the diameter increased from 5 to 30 mm. Upon presence of hole the SEA dropped sharply from 82 kJ/kg to 44 kJ/kg, but it fluctuated with the increase in the hole size. (4) The shape and distribution of the hole showed less influence on peak load and SEA compared to the hole size, which were fairly different from the perforated composite laminates. The increase in the number of holes along transverse direction influenced the peak load marginally but SEA considerably. (5) Both the strain gauges and finite element analysis results exhibited a strong concentrations of shear stress and shear strain around the holes, causing the mid-height collapse of tube. The finite element model was able to closely predict the locations of crack initiation (in the middle two edge for the circular and rhombus holes, two random hole corners for the square hole) and crack propagation on the perforated tubes, which demonstrated satisfactory correlation between the numerical prediction and experimental testing.