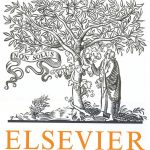
ترجمه مقاله نقش ضروری ارتباطات 6G با چشم انداز صنعت 4.0
- مبلغ: ۸۶,۰۰۰ تومان
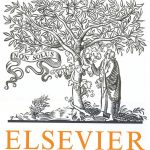
ترجمه مقاله پایداری توسعه شهری، تعدیل ساختار صنعتی و کارایی کاربری زمین
- مبلغ: ۹۱,۰۰۰ تومان
ABSTRACT
Incident involving failures of ASTM A53 carbon steel (CS) pipe, connected to pressure safety valve (PSV) and carrying raw gas has caused serious supply disruption. This study was performed to identify the most probable cause of the pipe failure. It was conducted by reviewing the existing design, construction data and pipe material analysis using nondestructive techniques such as VT, PT, MT and UT along with metallographic, hardness and microscopic analysis. The investigation revealed that excessive material loss has occurred in both failure and its adjacent regions due to abrasive grinding, resulting in the formation of a through thickness flaw. These grindings were performed to accommodate the preinstalled piping spool to avoid alteration in the pipe position. RCA demonstrated that this rapid thinning of the steel pipe body later led to its failure. Metallurgical study using photomicrograph shows that the morphology of the steel material was consistent and did not show any evidence of internal corrosion or micro fractures. Further damage to the surface of already excessively reduced thickness occurred due to nominal pipe vibration and atmospheric effect during service. The research work described in the paper has a significant meaning to recognize the root cause of such failures in CS pipes and through given recommendations to eliminate future such happenings.
6. Conclusion and recommendations
In reference to the existing evidence deduced from the tests and substantial existing data the study revealed that the root cause of the pipe failures is attributed to the initial leak of the raw gas pipe. From the basic pipe material properties and behaviour, it is suspected that the failure was initiated by a crack, most probably longitudinal in nature. The crack or horizontal slit allowed high pressure gas to jet through, with the jet momentum getting stronger as the effective diameter of the slit increased. Over time the crack enlarges and breaks off into large chunk, resulting in the gaping hole as evident in the phot record. In view of crack initiation and propagation, it is concluded that the root cause for the failure of the pipe section is due to excessive thinning as a result of thickness reduction by intentional grinding. Further damage to the surface of already excessively reduced thickness occurred due to nominal pipe vibration during service. Based on the above, it is recommended that during installation/fabrication of piping system, proper procedures may be implemented, followed by visual inspection through qualified inspector(s) including pre-service and in-service inspection.