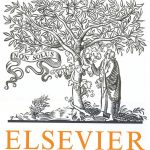
ترجمه مقاله نقش ضروری ارتباطات 6G با چشم انداز صنعت 4.0
- مبلغ: ۸۶,۰۰۰ تومان
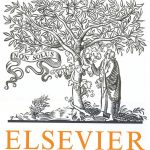
ترجمه مقاله پایداری توسعه شهری، تعدیل ساختار صنعتی و کارایی کاربری زمین
- مبلغ: ۹۱,۰۰۰ تومان
ABSTRACT
Additive manufacturing (AM) permits the fabrication of functionally optimized components with high geometrical complexity. The opportunity of using porous infill as an integrated part of the manufacturing process is an example of a unique AM feature. Automated design methods are still incapable of fully exploiting this design freedom. In this work, we show how the so-called coating approach to topology optimization provides a means for designing infill-based components that possess a strongly improved buckling load and, as a result, improved structural stability. The suggested approach thereby addresses an important inadequacy of the standard minimum compliance topology optimization approach, in which buckling is rarely accounted for; rather, a satisfactory buckling load is usually assured through a post-processing step that may lead to sub-optimal components. The present work compares the standard and coating approaches to topology optimization for the MBB beam benchmark case. The optimized structures are additively manufactured using a filamentary technique. This experimental study validates the numerical model used in the coating approach. Depending on the properties of the infill material, the buckling load may be more than four times higher than that of solid structures optimized under the same conditions.
5. Conclusions
It has been shown that the coating approach to topology optimization allows the exploitation of AM infill to create components that possess substantially improved buckling properties compared to those of structures that are optimized with the standard minimum compliance approach. In the specific MBB beam test case, the buckling load for the porous structure was more than five times that of the solid structure, for a decrease in stiffness of about 20%– 25%. This gain in buckling load is due to the porous infill, which leads to wider structural members and thus components with an inherently larger bending stiffness-to-weight ratio. The numerical results were backed by experimental measurements performed on additively manufactured test specimens. The measurement results were associated with some uncertainty, mainly because of rough assumptions on the material properties of the test specimens. However, the trends of the results are very clear, and the deviations are small compared to the performance differences. Going beyond the studied test case, a few remarks regarding relevance for future work should be stated. The porous component attained such a high in-plane buckling load that the structure was failure-limited by local buckling (due to a load concentration) rather than global buckling. More generally, local buckling failure in the infill is likely to occur before global buckling if the infill density is chosen to be too low. The out-of-plane buckling of the porous structure showed the need for designing experiments based on a full 3D structure. This study demonstrates how topology optimization may be adapted to AM-specific manufacturing opportunities and provide remarkable improvements in structural performance.