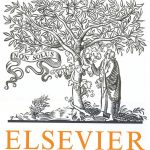
ترجمه مقاله نقش ضروری ارتباطات 6G با چشم انداز صنعت 4.0
- مبلغ: ۸۶,۰۰۰ تومان
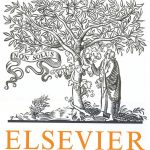
ترجمه مقاله پایداری توسعه شهری، تعدیل ساختار صنعتی و کارایی کاربری زمین
- مبلغ: ۹۱,۰۰۰ تومان
Abstract
Twin-roll casting is an energy-efficient technology for the magnesium strip production consisting of casting and rolling combined in one process step. Producing magnesium strips in an adequate quality-price ratio requires the application of material flow cost accounting to identify hidden improvement potentials. In the following, a material flow cost accounting analysis is carried out for the twin-roll casting process of AZ31 twin-roll-cast strips. Based on the findings, inefficient process steps of the twin-roll casting process are to be revealed, and actions for cost reduction from the point of a stable process management are to be assessed. Overall, an economic process and efficient material consumption can be designed for twin-roll casting considering the strip property development.
4. Conclusion and discussion
In this paper, a material flow cost accounting analysis was carried out for twin-roll casting of AZ31 twin-roll-cast strips. In this context, a valid model consisting of four submodels was developed to understand the environmental and financial effects of material and energy consumption. With respect to the results, it should be noted that the quantities and costs can only be applied to the pilot plant configuration. In addition peak prices were assumed and raw materials are subjected to fluctuations. In case of an industrial production, the consumptions and production costs will be further reduced based on extended production campaigns and quantity discounts for the required inputs. However, the results of the material flow cost accounting analysis illustrated that the twin-roll casting process is a resource-efficient and economic process despite short production runs. Moreover, it was shown how costs varied depending on the production volume. To further optimize the twin-roll casting technology, the steel casting nozzle was identified as a major cost driver. Options to achieve a price reduction are on the one hand improved manufacturing processes of the casting nozzle and on the other hand the development of production strategies using ceramic nozzles.