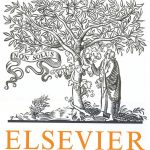
ترجمه مقاله نقش ضروری ارتباطات 6G با چشم انداز صنعت 4.0
- مبلغ: ۸۶,۰۰۰ تومان
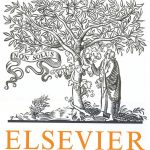
ترجمه مقاله پایداری توسعه شهری، تعدیل ساختار صنعتی و کارایی کاربری زمین
- مبلغ: ۹۱,۰۰۰ تومان
Abstract
Cordierite (2MgO·2Al2O3·5SiO2) is a thermal resistant ceramic presenting both low thermal expansion and electrical conductivity along with good chemical and mechanical properties. Thereby, it is suitable as material for manufacturing electric insulators, catalysis, refractory and porous ceramics. Solid-state reaction is the most common method for cordierite preparation. For this purpose, different mixtures including clay, alumina, talc, sand, diatomite and gibbsite are used. The present study is devoted to the preparation of cordierite-based materials using two mixtures of kaolin, talc and bauxite. Hence, prismatic specimens were shaped and tested to uniaxial compressive strength and heated in the range of 1200–1400 °C. The fired specimens were investigated via X-ray diffraction, Fourier transform infrared spectroscopy and scanning electron microscopy. Also, physical (firing shrinkage, water absorption, bulk density) and mechanical (bending strength) and dielectric properties of the fired bodies were measured as a function of temperature. The results showed that the fired bodies of the mixture composed of 50% by mass of kaolin, 20% by mass of talc and 30% by of mass of bauxite together with high sintering temperature (1400 °C) resulted in the formation of abundant amount of cordierite in conjunction with mullite, cristobalite and pseudorutile. Also, there was increase of firing shrinkage, bulk density and bending strength. These changes were essentially linked to amount of new phases that were formed. Water absorption declined with increase of sintering temperature which was related to the reduction of porosity due to the formation of vitreous phase. The mixtures of kaolin-talc-bauxite which were fired at the range of 1300–1400 °C exhibited dielectric constant values varying between 20.3 and 2.8 along with dielectric loss tangent which varied between 0.1316 and 0.0002 at room temperature of the laboratory. The two mixtures can be considered as promising materials for both ceramic and electronic applications.
4. Conclusion
Samples of two mixtures of raw materials (kaolin, bauxite and talc) were performed and fired in the range of 1200 – 1400 °C in order to get cordierite based ceramics. SEM images of the samples sintered at 1200 °C exhibited heterogeneous and sponge-like aspect which leads to fire bodies with high water absorption and low bulk density. As the temperature increased, fired bodies became compact and the shapes of pores changed. The mixture with great amount of talc led to the formation of fired bodies whose cordierite was the main new mineral and which did not contain mullite. Conversely, the mixture which contained great quantity of kaolin and low amount of talc resulted in fired bodies with abundant quantity of cordierite along with mullite. Bulk density and bending strength reached the maximum values (2.63 g/cm3 and 30 MPa respectively) around 1300 °C. Dielectric constant values varied between 20.26 and 2.80 whereas dielectric loss tangent were between 0.1316 and 0.0002 at ambient temperature. Anyway, cordierite bodies produced from mixtures of kaolin-bauxitetalc are promising materials for both ceramic and electronic applications.