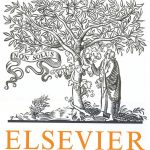
ترجمه مقاله نقش ضروری ارتباطات 6G با چشم انداز صنعت 4.0
- مبلغ: ۸۶,۰۰۰ تومان
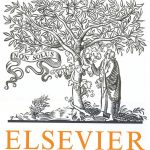
ترجمه مقاله پایداری توسعه شهری، تعدیل ساختار صنعتی و کارایی کاربری زمین
- مبلغ: ۹۱,۰۰۰ تومان
Abstract
Control surface, which is often located in the trailing edge of wings, is important in the attitude control of an aircraft. However, the efficiency of the control surface declines severely under the high deflect angle of the control surface because of the flow separation. To improve the efficiency of control surface, this study discusses a novel flow control technique aimed at suppressing the flow separation by pulsed blowing at the leading edge of the control surface. Results indicated that flow separation over the control surface can be suppressed by pulsed blowing, and the maximum average pitching moment coefficient of the control surface can be increased by nearly 90% when average blowing momentum coefficient is 0.03 relative to that of without blowing. Moreover, the lift coefficient of the control surface can be 95% times higher than that of without blowing, and the drag coefficient of the control surface can be reduced by 43% compared with that of without blowing. Finally, this study shows that the average blowing momentum coefficient and non-dimensional frequency of pulsed blowing are two of the key parameters of the pulsed blowing control technique. Both experimental and numerical simulations are used in this study. The experiment is completed in D-4 wind tunnel of Beihang University under conditions of Re 0.8×106.
4. Conclusions
Several conclusions are drawn based on the preceding analyses. This study introduces an innovative flow control technique, namely, pulse blowing technique. Evidently, flow separation can be suppressed by pulsed blowing and the control efficiency of the flap can be enhanced. With the increasing Str of pulsed blowing, the increment of lift and the magnitude of pitching moment increases gradually and a critical Str exist in which the increment of the lift and the magnitude of pitching moment coefficient reaches the maximum value. The critical Str is decided by the velocity of freestream and the geometry of model. The pulsed blowing effect is larger than that of continuous blowing when Str is larger than the critical Str. In the experimental test, the largest increment of the magnitude of pitching moment coefficient is obtained when Str is approximately 0.4 ( f = 40 Hz). This result shows that the increment of the magnitude of pitching moment coefficient with pulsed blowing is 26.7% larger than that of continuous blowing under the same blowing momentum, that is, Cμ = 0.011 and V∞ = 20 m/s. The maximum increment of the magnitude of pitching moment coefficient of pulsed blowing with Cμ = 0.011 is 72%, and the increment of the magnitude of pitching moment coefficient of continuous blowing with Cμ = 0.02 is 61%. Thus, by pulsed blowing, gas consumption is only 50% compared with continuous blowing, and another 11% increment of the magnitude of pitching moment coefficient is acquired. Therefore, pulsed blowing is an advanced control technique that can be used to improve the control efficiency of the flap.