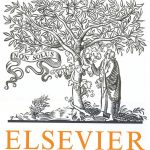
ترجمه مقاله نقش ضروری ارتباطات 6G با چشم انداز صنعت 4.0
- مبلغ: ۸۶,۰۰۰ تومان
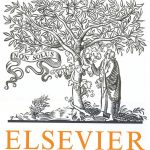
ترجمه مقاله پایداری توسعه شهری، تعدیل ساختار صنعتی و کارایی کاربری زمین
- مبلغ: ۹۱,۰۰۰ تومان
Abstract
This attempt proposes a Finite Element Approach (FEA) to investigate the tribological behavior of glass fiber reinforced polyester composite. The 3D finite element model was developed upon ABAQUS/Explicit. The Johnson-Cook criteria were considered for describing the material behavior and damage of both fiber and matrix phases. The fiber/matrix interface behavior was, however, modeled using a thin cohesive zone (CZ). A mixed-mode loading concept was specially adopted to predict delamination propagation within the interface. The prevailing wear mechanisms owing to Multi-Scratch Test (MST) were inspected at variable load and attack angle, using scanning electron microscope (SEM). Wear maps were built to highlight the correlation between friction coefficient and wear mechanisms. Predictions of both elementary and interacting mechanisms showed excellent correlation with observations. It was revealed that material removal process varies sensitively with the dominating failure mode. The proposed approach exhibits good ability not only in predicting active mechanisms but also in detecting damage sequences governing the surface integrity during scratching.
5. Conclusions
In this paper, the investigation of elementary wear mechanisms in both SST and MST were carried out. A numerical approach was specially proposed for better understanding of the evolution of damage mechanisms. Particular focus was put on highlighting the effect of mechanisms interaction in the material removal process. According to the findings, the following conclusions can be drawn. The SEM observations make it possible to distinguish the elementary mechanisms dominating the material removal process in SST and their limits of action when the testing parameters, namely, the attack angle and normal vary. Inspections of multi-scratched worn area reveal high sensitivity of surface integrity to dominant interacting mechanisms. When SST, the apparent friction displays high dependency on tribological parameters. However, it shows more sensitivity to the attack angle than to the normal load. An increase in the attack angle increases lapp, and switches the wear mechanisms from ploughing to fibers pullout and fibers fracture. The wear maps reveal that ploughing, fibers multi-fractures, and fibers fracture dominate within smaller domain in MST than in SST. However, the combined fibers fracture and fibers pullout dominant mechanisms occupy a larger domain in MST. Five domains were drawn in MST face to only four domains drawn in SST. Major mechanisms transformation was outlined for relatively high load and low angle ranges: The elementary fiber multi-fractures dominating in SST becomes acting in association with fiber pullout and mode II fiber failure in MST. The proposed models exhibit excellent ability to simulate damage mechanisms dominating material removal process in both SST and MST. Specially, the mixed-mode loading criterion shows high efficiency to predict delamination propagation in the CZ. Decidedly, SEM inspections confirmed the numerical results. In fact, the MST model demonstrates ability to predict mechanisms’ interaction together with sequences of material removal process in GFRP composite.