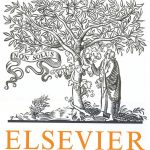
ترجمه مقاله نقش ضروری ارتباطات 6G با چشم انداز صنعت 4.0
- مبلغ: ۸۶,۰۰۰ تومان
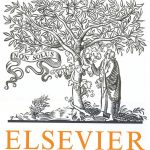
ترجمه مقاله پایداری توسعه شهری، تعدیل ساختار صنعتی و کارایی کاربری زمین
- مبلغ: ۹۱,۰۰۰ تومان
Abstract
Finite element analysis (FEA) of structural composites is mostly based on an as-designed geometry and input data. As-designed input data do not consider the manufacturing processes. For an as-built structural simulation of composites, it is important to integrate manufacturing process data into the structural analysis. Therefore, mapping algorithms are needed to transfer and process data between different process and structural simulation steps considering the application of different finite elements and media discretization for the individual simulation steps. This paper considers a mapping algorithm based on a bucket sort algorithm, shape interpolation functions of finite elements and internal fiber architectures of composite materials with a subsequent material properties prediction. The proposed algorithm is applicable for unidirectional composites as well as for non-crimped, woven and braided fabrics. Particular, it is shown how fiber orientation, as vector value of finite elements, is sensible for a data transfer between meshes with out-of-plane material defects. This integrated simulation approach is applied on a generic demonstrator geometry and aerospace component geometries. The implementation is realized within a new developed simulation platform for composites structures, from process up to structural simulations
5. Conclusion
Process simulations of composite structures are seaming less integrated into structural analysis. This paper presented mapping algorithms with the focus on fiber orientation transfer for UD, NCF, woven or braided fabrics and subsequent material properties prediction between incompatible meshes. A definition of the fiber orientation needs a reference system that can be changed from mesh to mesh. Incompatible meshes from draping and structural analysis are discussed. Only the transfer of FE data is not sufficient for a realistic structural analysis and the subsequent design of complex components with e.g. draped UD, NCF, woven and braided fabrics. Stiffness predictions based on shear angle and thickness variation is shown with an extended validated analytical approach for the sheared woven composite materials.