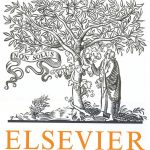
ترجمه مقاله نقش ضروری ارتباطات 6G با چشم انداز صنعت 4.0
- مبلغ: ۸۶,۰۰۰ تومان
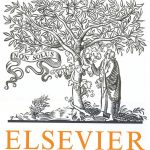
ترجمه مقاله پایداری توسعه شهری، تعدیل ساختار صنعتی و کارایی کاربری زمین
- مبلغ: ۹۱,۰۰۰ تومان
Work has been carried out using an optical seal specific rig simulating the high pressure working conditions that a reciprocating seal encounters. The rig has provided friction measurements using transducers while simultaneously providing detailed 2-D contact images using a boroscope optical arrangement. The effect of pressure and stroking velocity on the friction of the seal is studied. Other effects such as complex flow patterns, leakage and wear in the seal contact are observed and discussed. It is found both through measurements and images that high pressure conditions encourage the development of thicker films and more effective lubrication takes place at higher pressures. The effect of speed is not significant for the range of speeds in the tests.
Particularly of concern are actuator start-up and slow-down cycles when surface adhesion effects lead to high friction. These conditions are present in real applications and the overall reliability of the seals is dictated by these cycles.
1. INTRODUCTION
Linear hydraulic actuators are employed in several engineering applications as a means of transferring large forces using pressurised fluid systems. The sealing of such high pressure systems is done using elastomeric seals. The seals under study here are specifically dynamic rectangular elastomeric seals, which experience motion against the actuator surface while maintaining a seal against pressure differentials. In conditions where safety is of paramount importance the safe and reliable operation of such seals is critical.
4. CONCLUSIONS
Experiments have been carried out using a novel optical rig that provides images of a gland seal in contact with a glass tube while simultaneously providing 2-D images of the contact itself.
When the actuator is left standing the seals natural tendency is to squeeze fluid out of the contact. Such almost dry contact conditions are encountered right when the actuator is started after a rest period. Seal friction in these cases can be expected to be maximum since surface adhesion forces have to be overcome to get relative motion.