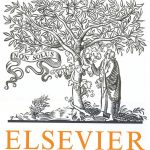
ترجمه مقاله نقش ضروری ارتباطات 6G با چشم انداز صنعت 4.0
- مبلغ: ۸۶,۰۰۰ تومان
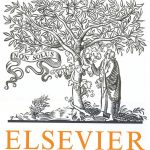
ترجمه مقاله پایداری توسعه شهری، تعدیل ساختار صنعتی و کارایی کاربری زمین
- مبلغ: ۹۱,۰۰۰ تومان
Abstract
A wind turbine blade design inspired by a tree seed called Triplaris Americana is presented. The blade was designed by means of an analysis of the seed’s curvature and airfoil along its wingspan; the result is as a non-conventional horizontal axis wind turbine composed of three blades. A computational fluid dynamic simulation was performed in order to estimate the operational loads. The blade’s structure was designed by means of composite structural design, resulting in six zones with different laminates of carbon fiber. The balance of the aerodynamic and inertial loads was achieved in order to guarantee a minimum change in blade’s geometry to prevent a performance reduction. Finally, a manufacturing simulation by means of vacuum assisted resin infusion was performed. Four injections strategies were proposed with three of them considered successful based on a complete mold filling and the time limit imposed by the polymerization time of the resin.
Conclusions
The aerodynamic design started from a previous study where a practical geometry was proposed to generate clean energy, where the wind turbine model was validated aerodynamically with errors below 8%. That allowed to obtain the pressure profiles to analyze the forces and torque to know the operational conditions of the wind turbine. The mechanical properties of the reinforced gave the material limitations and therefore the strain distribution. There were proposed several zones with different laminates in order to withstand the forces induced by the operational loads and to obtain a maximum displacement of 31.1 mm at the blade’s tip. In this way, the aerodynamic performance is not affected in a substantial way. Also, the stacking sequences were considered symmetrical and balanced to minimize coupling effects that could affect the blade shape. For such a complex shape, it was necessary to perform a study to analyze the resin flow behavior involving all the stacking sequences and considering the permeability changes over the reinforcements, since any change in this parameter can lead to greater changes in the flow front. The permeability was characterized for two types of one single reinforcement ply and then the overall permeability of the laminates was approximate in the software considering the number of plies and the thickness. The injection strategies gave an idea of how the resin will behave and the pressure and time requirements to complete a full impregnation. Several strategies were studied based on a straight blade shape, however, the results were unsatisfactory since gravity effect was neglected and the resin behavior break the limit imposed by time and filling, for this reasons those strategies were not included in this study. The strategies that were proposed considered a resin fluid front that flows against gravity in order to avoid additional accelerations that might leave air entrapment zones.